The process of powder coat castings enhances durability and visual appeal of precision casting metal parts by applying a specially formulated dry powder that is then cured under heat to create a uniform, hard finish.
Shelmet
PO Box 95
550 County Highway GH
Wild Rose, WI 54984
Mon - Fri 7.00 - 4.00 CST OPEN
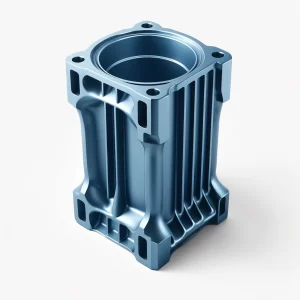
Protection & Aesthetic Appeal
Powder coating provides a protective and decorative finish to a wide range of materials, utilizing a dry powder that is free from solvents. This method offers improved durability, corrosion resistance, and a wide choice of aesthetics due to its ability to produce many colors and textures.
Powder Coating Process Specific Use Benefits
- Durability: Highly resistant to chipping, scratching, and wearing compared to other finishes.
- Aesthetic Variety: Offers an unlimited range of colors and textures, enabling customization to specific design requirements.
- Corrosion Resistant: Provides excellent protection against environmental elements.
- Cost Effectiveness: Less waste produced during application, reducing overall material costs.
Shelmet provides a seamless movement from design to final product with exacting precision. Particularly, we focus on technical accuracy that achieves ISO 9001:2015 standards. Shelmet emphasizes quality into every stage of your investment casting project.
Powder Coat Castings
Precision Investment Casting
Get specific casting process answers at no charge from a Shelmet metal casting expert Help Line.
920-622-3344
A Visually Appealing & Durable Protective Surface Layer
Powder coating applies a finish that not only enhances the visual appearance of metal parts but also provides an added layer that protects against harsh conditions. The cured layer formed is uniform and bonds strongly with the metal substrate, ensuring long-lasting performance.
Why Choose Powder Coating Over Other Methods
Other finishing techniques like painting do offer aesthetic options, but the bonding of powder coating stands out for its durability.
This investment casting finishing process is suited for a broad range of industrial and consumer applications.
Enhancing Castings with Powder Coating Color
Powder coating excels in producing vibrant and diverse color finishes, which not only improves functionality but also boosts the visual appeal especially in sectors like automotive and consumer electronics. An added benefit is the increased resistance to fading under continuous use, maintaining aesthetic integrity.
Powder coating provides excellent advantages, but there are limitations:
- Complex Geometries: Highly intricate designs may challenge the uniformity of the coat.
- Color Matching: Achieving precise color matching can be difficult across different batches.
- Fading with UV Exposure: Similar to anodized colors, vibrant powder coated colors can also fade over time when exposed to UV light. However, the quality of the powder and the use of UV-resistant formulas can mitigate this fading.
Powder coating enhances resilience of investment castings against several challenging conditions:
- Corrosive Environments: Powder coatings are highly effective in resisting corrosion from chemicals, moisture, and salt air, making them suitable for use in marine, industrial, and coastal environments.
- High-Temperature Settings: Certain formulations of powder coatings can withstand high temperatures, making them ideal for components used in engines, heat exchanges, and other high-heat applications.
- Mechanical Wear: The tough, durable surface of powder coated parts resists scratching, chipping, and abrasion, which is essential for parts used in high-contact or high-wear scenarios like tools and machinery.
- UV Exposure: While UV rays can cause some colors to fade, UV-resistant powder coatings maintain their color and integrity even in prolonged sunlight, which is crucial for outdoor furniture, automotive parts, and exterior architectural elements.
- Extreme Weather Conditions: Powder coat castings can endure severe weather conditions, including extreme cold and hot temperatures, making them suitable for outdoor structures and equipment exposed to the elements.
These properties make powder coated investment castings highly dependable for use across many demanding applications in most industries.
Powder coat castings have enhanced chemical resistance that ensures they can withstand demanding environments.
- Durability: Provides a long-lasting finish that resists environmental and mechanical wear.
- Visual Appeal: Allows for a high degree of customization in finish and color.
- Improved Adhesion: Supports excellent adhesion to metal substrates, necessary for secondary processing like painting.
- Ease of Application: Simplifies the finishing process with quick application and curing times.
- Color Availability: Powder coating can produce a white finish, unlike anodizing. It offers a broader range of colors, including very bright and pastel shades, making it a versatile option for color-specific applications.
How do I choose the right metal or alloy for my project?
Questions? Call Shelmet customer service.
(920) 622 -3344 Call Today!
We offer free alloy and process recommendations based on your project requirements, desired mechanical properties, and budget considerations. Very often we save our customers much time and casting costs.
Ask Your Shelmet Metal Casting Expert How Powder Coating Steels, Aluminum or other metals and alloys Can Benefit You
Performance characteristics of a powder coated investment casting depend on the specific powder coating formula used, as well as the base metal. For example, thermoset powders can provide a highly durable finish that is excellent for wear resistance, while thermoplastic powders might offer superior flexibility and impact resistance.
Each powder type brings its own advantages that alter the aesthetics, environmental tolerances, and mechanical properties. Your Shelmet metal casting expert can guide you in selecting the right powder coating to achieve the desired benefits for your project.
01. What is the powder coating process?
Powder coating involves applying a dry powder onto the metal surface electrostatically, followed by curing it in an oven to form a durable coat.
02. Can powder-coated finishes be customized?
Yes, powder coating offers a wide range of colors and textures.
03. How durable is the finish on a powder coat casting?
Extremely durable, providing excellent resistance to wear, corrosion, and fading.
Wear Resistance for Every Setting
- Everyday Use: Even in less demanding indoor environments, powder coatings on investment castings hold up beautifully, resisting scratches and chips for up to 7 years. Common coating choice for home and office furnishings.
- Optimized Durability: In environments where conditions are controlled and the highest quality powders are used, excellent performance up to 20 years.
Corrosion Resistance That Remains With Useful Metal Part Life Expectancy
- Challenging Environments: In areas exposed to harsh elements without the necessary pre-treatments, powder coatings work against corrosion for up to 3 years. An excellent choice for industrial applications needing frequent updates.
- Maximized Protection: Today’s advanced formulated coatings make metal investment casting parts able to remain corrosion resistant for possibly as long as 20 years, especially in milder conditions. Parts such as commercial fixtures and decorative wall structures maintain their appearance.
Fade Resistance
- Sunny Exposures: For items in bright, sun-soaked locations, modern UV-stable powder coatings maintain vibrant colors and gloss for up to 7 years without significant fading. Outdoor low-traffic installations such as display assemblies and playground equipment.
- Lasting Brilliance: In areas with moderate sunlight, expect the hues and shine of powder coated metal investment castings to look as new for up to 15 to 20 years. Architectural features and vehicle parts benefit with specific powder coatings.
How Can Shelmet Investment Casting Coating Solutions Assist Your Project?
Each application and environment is unique, and so are your needs. The importance of matching the right powder coating to your specific project and conditions can ensure optimal durability and appearance. You Shelmet metal casting can help discover the best process for your investment casting parts.
04. What types of metals can be powder coated?
Almost any metal including aluminum, steel, and iron can be effectively powder coated.
05. Can I apply powder coating to a part that has been previously coated?
Yes, with proper surface preparation, powder coating can be applied over existing finishes.
“We Do What We Say We Will Do.”
Customers know what to expect from Shelmet at the onset of the investment casting project and on through to delivery.